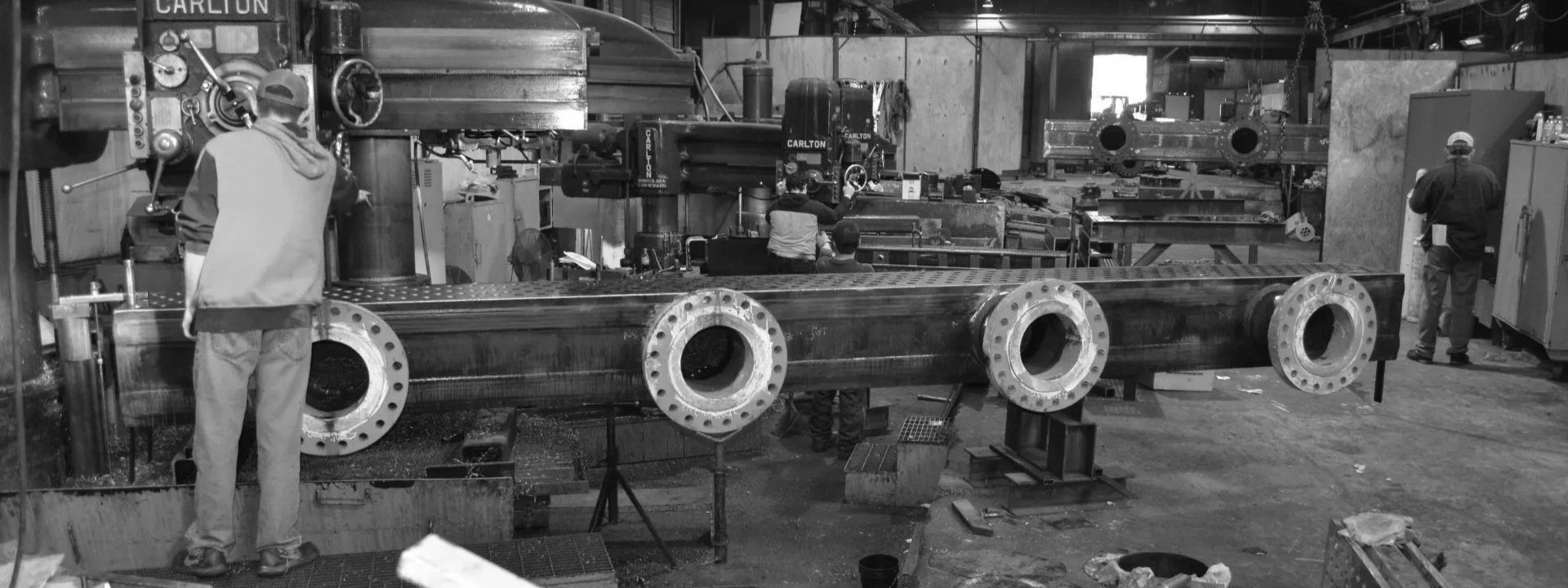
Products
Bosetech’s heat transfer products focus on carbon reduction solutions for the industrial sector
-
In applications where there are no available heat sinks, heat can be managed using air coolers. Process fluid is cooled using ambient air. Our air coolers routinely outweigh the competition. Our structural design, fan and drive system are strong and robust, further reducing vibration and rotating component wear.
-
Our Waste Heat Recovery products are designed to capture exhaust heat and reuse it, increasing efficiency of the overall system. There are 3 main categories of products: (1) Economizers (2) Exhaust Heat Recovery (3) Exhaust Steam Generators.
Waste heat is captured from the exhaust streams and transferred to fluids known as heat sinks. Exhaust can be captured from various combustion sources such as natural gas, propane, digester gas, diesel fuel and light to heavy fuel oils. The cooled exhaust can then transfer to other emission reducing processes such as carbon capture systems. Waste heat is transferred to heat sinks such as water, glycol, thermal fluids or to produce steam. -
There are 3 main categories of strainers in our portfolio; Simplex, Duplex and Automatic Self-cleaning Strainers.
Simplex strainers can be cast, welded or machined. They come with flange connections or female pipe threaded connections. They can be used to filter water, oil, fuels and gases.Duplex strainers allow flow to be diverted without disrupting operations. We offer cast and welded models, with a number of closures types.
The self-cleaning mechanism uses the Bernoulli principal for contactless cleaning. The waste is flushed via the flushing outlet. Timing is triggered by a timer, differential pressure sensor, button on local or remote control.
Air Coolers
There are two main categories of air cooled heat exchangers: Dry Coolers and Wet Coolers. The main components of an air cooled exchanger are a tube bundle and a fan. The tubes contain process fluid and the fan blows air over the tubes, cooling the process fluid and rejecting heat to the atmosphere.
DRY COOLER tube bundles are built using extended surface area finned tubes. The process fluid is cooled within a close approach to the dry bulb temperature.
WET COOLERS are build using bare tube bundles. Process fluid within the tubes are cooled by simultaneously spraying them with water and blowing air. This is a process known as evaporative cooling, in which the process fluid is cooling within a close approach to the wet bulb temperature.
HYBRID SOLUTIONS use dry air coolers and evaporative coolers in tandem to achieve the best heat rejection performance.
Dry Air Cooled Exchanger
Evaporative Cooler
Waste Heat Recovery
There are 3 main categories of waste heat recovery products: Boiler Economizers, Exhaust Heat Recovery (for liquids), and Exhaust Steam Generators. The principal of waste heat recovery is based on hot exhaust (or flue gas) passing through a chamber over a tube bundle. A tube bundle is built with brazed finned tubes; The materials depend on the exhaust temperature profile. The tubes carry thermal fluid (water, glycol, oil), which cool the exhaust and capture the heat. The captured heat energy can be used to produce steam, provide heat to process areas. Waste Heat Recovery reduce fuel consumption, carbon emissions and generate cost savings.